Digital Disruption in the African Construction Industry
State-of-the-art technologies are bringing about a digital shift in the African construction industry.
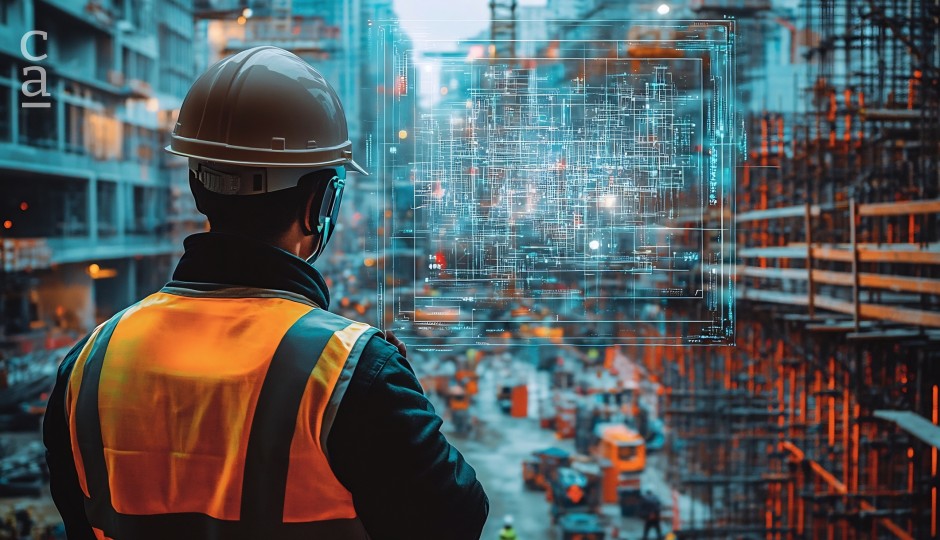
A booming population and expanding urbanisation in Africa have spawned the need for growth in the infrastructure sector and construction industry.
According to the African Development Bank (AfDB), 350 million people will be added to Africa's urban population by 2030, making the continent the fastest-urbanising in the world. This calls for rapid technological advancements that can radically transform the construction landscape by reducing costs, increasing efficiency and reducing project delivery times.
The African construction industry stands at the cusp of digital transformation. State-of-the-art technologies such as artificial intelligence (AI), building information modelling (BIM), drones and augmented reality/virtual reality (AR/VR) tools are bringing about a digital shift in the continent’s construction industry. The integration of such technologies would entail moving from blueprints to bytes, from sites to simulations, and from bricks to clicks - marking a significant revamping of how projects are planned, designed and executed.
Across most, if not all, of our projects at Linus International, we have employed technologies to automate client, contractor and supplier coordination and communications. These range from using collaborative design boards to installing cameras to provide by-the-minute progress status and reports.
For our projects in Africa, technology becomes far more critical, and often indispensable, as we funnel site and project information and progress reports back to the head office in Dubai. This information would be parsed through by our projects team and senior management to enable immediate corrective actions wherever necessary. For companies that operate across multiple jurisdictions and sites, this strategy sometimes becomes critical within the same country itself.
In today’s digitally automated world, it has become necessary to embrace cutting-edge technologies in an evolving and competitive industry where precision, efficiency and safety are paramount. Using time-lapse videography, BIM, drone fly-bys and interactive walkthroughs, we are able to turbocharge our marketing efforts while using real-time progress tracking to monitor construction speed.
Building Information Modelling (BIM)
BIM, for example, allows stakeholders to view the physical project digitally, thus providing an overall visualisation of the infrastructure and eliminating potential errors.
For warehouse projects, which are bound by strict completion deadlines, it is imperative we meet the tenant’s requirement of taking possession. Responding to delays promptly by addressing concerns noticed through our tracking system, we are able to offset delays far quicker than we could in the past. Time is literally money in this case.
Use of Drones
Time-lapse and drone photography have transformed our large-scale warehousing projects. Considering the size, scale and remoteness of projects, such photography often provides immediate updates from sites. Most importantly, in the case of execution of projects for other customers, time-lapse photography/videography also provides a holistic view of the progress achieved when it often is not apparent prima facie.
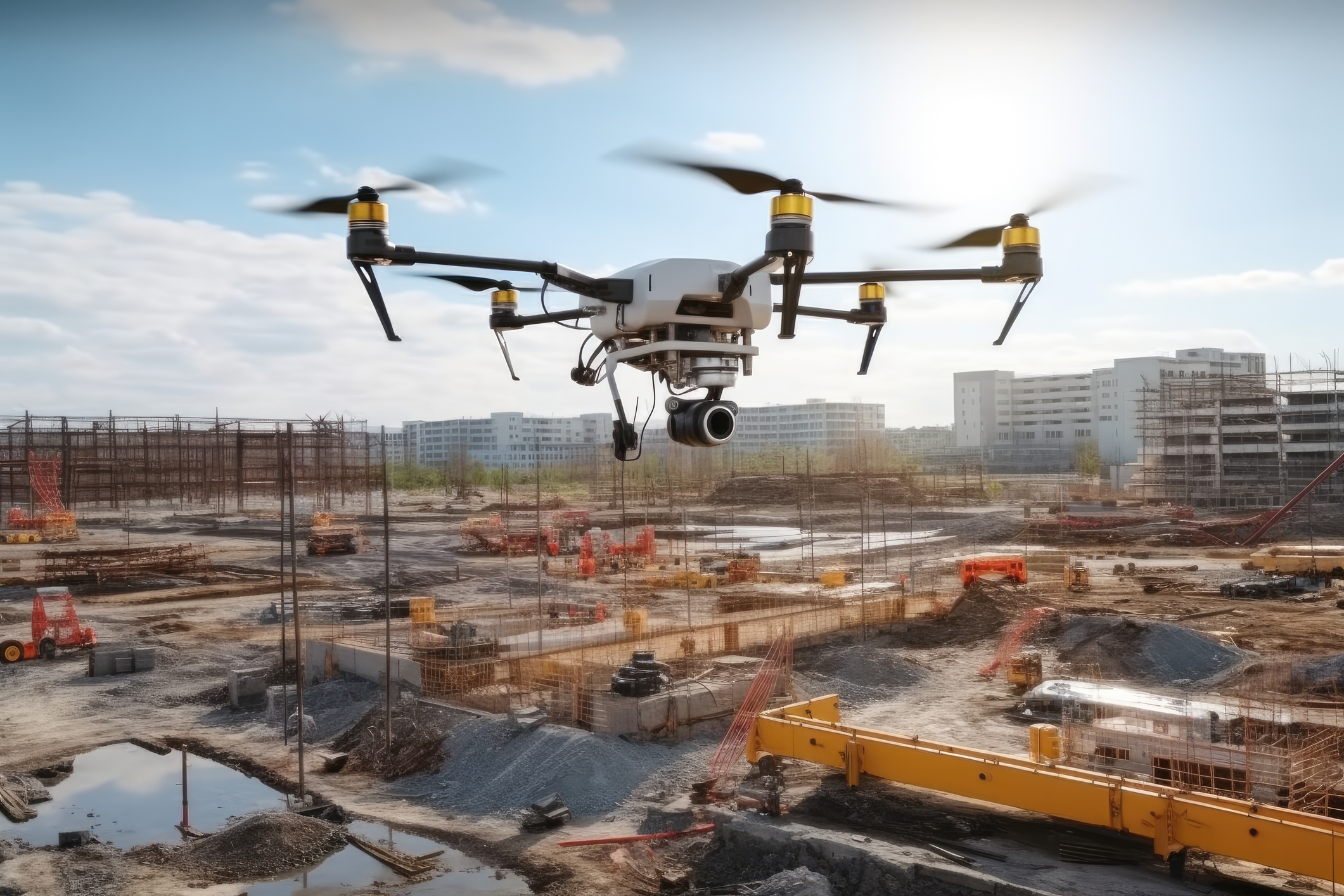
Such technological breakthroughs mark a paradigm shift from traditional methods of construction. They expedite the construction process, leading to a remarkable reduction in construction time, compared to time-consuming legacy processes and conventional tools. Drones such as the ones we have begun to use across our projects facilitate an aerial view of the site from a vantage point and provide real-time visibility, which aids in monitoring progress, enables quick decision-making and reduces delays. Compared to traditional methods, drones are capable of inspecting areas that are inaccessible to humans, ensuring the safety of workers and providing accurate data.
Other Transformative Technologies
Meanwhile, technologies such as 3D printing create structures in a way that drastically reduces waste and, thus, costs. AR and VR are also critical tools in the construction toolkit that offer an immersive experience in a simulated environment. This enables stakeholders to explore projects virtually to troubleshoot issues early on.
Similarly, transformative technologies such as AI, robotics and automation can optimise construction planning, cost estimation and risk analysis, thereby accelerating growth in the construction process. Automation technologies implemented over the course of years enabled our manufacturing unit to employ higher precision manufacturing of joinery, woodwork and metal features that traditionally recorded higher instances of rework. Machine automation has reduced human errors and imprecise measurements that famously led to the ‘garbage-in, garbage-out’ scenario.
The Internet of Things (IoT) has also supercharged equipment monitoring and data collection. Our scaffolding division has only recently begun its first initiative of employing IoT for truck movement, stock deliveries, scaffolding erection speed and progress. This has enabled us to provide granular-level updates to our clients across projects, both small and large. This reduces the cost of monitoring, historically done manually, and dramatically reduces man-made errors.
As our logistics network has expanded, more vehicles have been introduced into the fleet to cater to our growing needs. More importantly, we ehave stablished four new depots to support our main hub in Dubai. Using fleet management software, internet-based trackers and smart allocation tools, we are able to dynamically dispatch vehicles loaded with stock depending on a variety of factors such as distance of site, closest depot with available stock and highest efficiency in fuel costs by managing traffic and vehicle selection.
A Green Future
The construction industry in Africa can play a significant role in paving the way for a green future. By ensuring proper waste utilisation, resource management and energy efficiency, technology can also help reduce pollution. Investing in technology can prove to be a smart move in the journey towards a sustainable future.
To cite an example from Linus International's experience, on our journey towards becoming a global enterprise, our interior fitout division embarked on a flagship fitout project in Kinshasa. We faced significant cross-continent execution challenges from timeline management, logistics and clearances, quality control, off-site execution and delivery, and legal challenges.
Waste creation through execution and inefficiencies became a major concern. In response, we launched various landmark pilot initiatives that allowed us to control waste through modular design and packaging/assembly done through state-of-the-art modelling software, as well as employing video monitoring to track hour-by-hour changes to the site.
Using modular design software, we managed to repurpose cut pieces and waste material into other aspects of the design. This is quite similar to the design methodology used by IKEA in its self-assembly furniture for personal use.
Additionally, we employed a tongue-and-groove jointing system, again enhanced by the use of advanced computer-aided design (CAD) systems, to dramatically reduce the use of nails and screws, unless necessary. Such software also allowed us to increase precision and avoid dependencies on ‘tolerances’ that were often maintained for ‘incidental’ errors during manufacturing and installation.
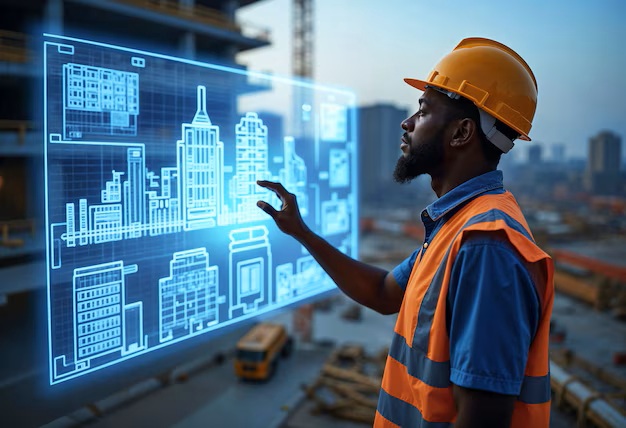
The future was, is and will be technology. The integration of technology into the construction industry is not just a choice anymore; it has become the need of the hour. Embracing the use of technology offers a unique opportunity for Africa to bring about meaningful change in the industry and to position itself as a potential leader on the global stage.
Top photo: Construction manager using AR/VR technology onsite (© Chumporn Chophwan | Dreamstime)
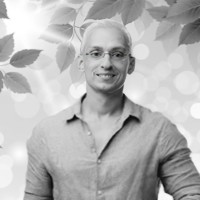
Sumit Pathak is the CEO of Linus International FZCO, based in Dubai.